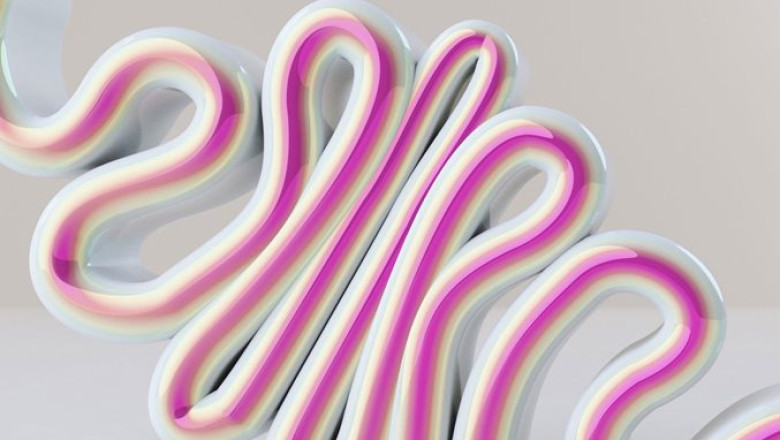
views
Building value-chain resilience with AI
Across industries, value chains are facing increasing uncertainty from climatic anomalies, market volatility, and the COVID-19 pandemic, among other factors. Industries as diverse as agriculture, oil and gas, and mining face essentially the same problem: they need the ability to both run with increased efficiency and recover quickly from unforeseen or unexpected challenges. But these two goals often conflict. If companies simply increase production levels, they’ll inevitably run into bottlenecks—and if failures occur that worsen those bottlenecks, the entire network can slow down and become less resilient. 1
1. For more on how COVID-19 has affected supply chains, see Knut Alicke, Richa Gupta, and Vera Trautwein, “Resetting supply chains for the next normal,” July 21, 2020.
Resolving this conflict presents several challenges. Organizations often make local decisions in silos without considering downstream implications, which requires downstream operators to manually request adjustments upstream as they discover challenges. Although digital technologies can improve resilience by assisting decision making, achieving transparency across the value chain requires the alignment of many stakeholders and diverse expectations about what the technologies should deliver.
This article is a collaborative effort by Valerio Dilda, Rajat Gupta, Axel Karlsson, Lapo Mori, Sebastian Reiter, and Saveliy Vasilev, representing views from McKinsey’s Basic Materials Practice.
Increasingly sophisticated artificial intelligence (AI) technologies—such as advanced analytics-based forecasting, digital-twin supply-chain simulations, and supply-chain optimization tools—can help companies improve the resilience-efficiency balance of their value chains. We analyzed more than 50 technology-driven supply-chain transformations and distilled three key factors of success in implementing and adopting digital supply-chain technologies: value-driven solution design, enhanced business process and capability building, and seamless technological implementation.
In any industry, value-chain conditions change every day. In the rail industry, for example, extreme weather events such as floods and wildfires have had a direct impact on local supply chains over the past year, causing companies to rethink their operation strategies. Even in nondisrupted scenarios, conditions are challenging because of mundane factors such as equipment outages, unexpected demand shifts, transportation issues, and upstream plan delays.
Coping with this dynamic in an intrinsically uncertain environment can be difficult. The probabilistic nature of value chains must be accounted for in any strategic and operational initiative. Further complicating matters, processes must be continually updated and people reskilled. AI technologies can effectively deal with complexity, helping organizations keep up with changes, mitigate risk, and create value. In fact, our research indicates the average bottom-line impact of successfully implemented supply-chain digital transformations is between two and five percentage points of earnings before interest, taxes, depreciation, and amortization (EBITDA) margin.
AI technologies can effectively deal with complexity, helping organizations keep up with changes, mitigate risk, and create value.
Value-chain resilience is the ability to recover quickly and gracefully from challenges. It can be achieved by improving end-to-end processes (to ensure decisions are considered within a broader context), deploying asset capacities across the value chain (such as adding warehouses and trucks as necessary), and deploying planning capabilities that incorporate these uncertainties (a single source of truth and AI-powered optimization models). Over the past year or so, the COVID-19 crisis has highlighted the critical importance of the ability to react to unforeseen events effectively while sacrificing as little value as possible.
Often, the challenge is to align players across the value chain on end-to-end trade-offs in a fact-based way. On this point, value-chain owners looking to increase efficiency and resilience must tackle the following tasks:
The next generation of end-to-end planning processes will be fundamentally different from today’s. AI can help balance efficiency and resilience by incorporating uncertainty into realistic simulations of reality to help organizations evaluate scenarios and identify risks. AI can also find optimal plans for different time horizons. In doing so, it can recommend operational decisions that balance cost with revenue and provide real-time end-to-end visibility to better anticipate and react to supply-chain disruption.
All three approaches can individually create significant value and are part of the transformation journey. However, value and resilience are only maximized when they are fully integrated. In agriculture, for example, an AI-based forecasting process can evaluate cost, revenue, service, and inventory implications at the outset of the crop-growth process. From there, a digital twin (a virtual representation of the value chain) can help identify risks and increase crop protection. Global suppliers can use AI-planning optimization to extract active ingredients from crops and deliver these ingredients to formulation facilities, where they are combined to create products. Afterward, an optimized supply-chain network can distribute these products to distributors and retailers in the most efficient way. Finally, each step can be monitored in real time with control towers to respond to any unforeseen disruptions or constraints—such as extreme weather events or supply limitations—and ensure smooth product deliveries.
As one example, a simulation can help operators understand the impact a railway outage would have on the rest of the value chain and determine the best mitigation action (Exhibit 1).
The digital twin is given the outage information, a set of “runs” are performed, and the output KPIs are presented by a set of dashboards. Given the outage, operators will likely see that the expected overall throughput KPI is lower than planned.
Since the value chain has some built-in resilience by design, the operators can evaluate alternative mitigation plans. For instance, they may consider renting extra capacity on another rail connection. To evaluate this idea, they can enter new parameters into the simulation aiming to capture the “fix,” then run the simulation again. If the fix improved the throughput KPI, then the operators know renting extra capacity will help mitigate the rail outage.
We strive to provide individuals with disabilities equal access to our website. If you would like information about this content we will be happy to work with you. Please email us at: [email protected]
Simulations are descriptive analytics tools. In a simulation, a digital twin is constructed with uncertainty measures and operational inputs. Next, a number of simulations of the future are performed using this digital twin and a summary is presented to the user for analysis. The end result—a set of key performance indicators (KPIs) describing current challenges—helps companies build resilience in the current environment.
In this sense, simulations can help identify and analyze root causes of bottlenecks. This is particularly important when responding to choke points in the system that vary over time, including changing operating conditions, maintenance downtime, weather conditions, or third-party dependencies. Simulations can also analyze the impact of strategic decisions across the value chain, such as the decision to close or open a location, build new storage buffers, or make capital expenditures.
Once planning is implemented, operators follow the planning-cycle process outlined below, either on a day-by-day basis or over the course of several months (Exhibit 2).
To build an optimization scenario, the user creates a snapshot of the current value chain by reviewing and adjusting live data on current demand, production capacity, and price information. Once the inputs match the planner’s requirements, an optimization model is executed to determine an optimal solution.
If the planner is ready, the model's suggestion can be implemented. However, if the planner spots an issue—for example, a significant delay due to a shortage caused by a production schedule—the planner can address the production targets and rerun the optimizer.
Organizations implementing such systems can generate and discuss more than ten scenarios in a live one-hour call with many stakeholders—for example, port operators might discuss delivery times with a manufacturing plant. In each cycle iteration, the AI chooses an optimal plan, eliminating millions of suboptimal plans that would perform worse on efficiency or resilience KPIs.
We strive to provide individuals with disabilities equal access to our website. If you would like information about this content we will be happy to work with you. Please email us at: [email protected]
Optimization models are prescriptive analytics tools. The main output is an optimal execution plan for the current environment, in which decisions are made accounting for the end-to-end impact. Given operational considerations, an optimization model finds the optimal plan. These considerations capture the current operational conditions, a detailed view of how the supply network functions, and can include uncertainties about the future.
Such models are ideal for improving operational and commercial decisions. For example, a mining company faced operational challenges across the mine-to-market value chain. Its siloed operating model lacked an end-to-end optimization engine, which would have proposed an optimal production plan, vessel schedule, product blend, and train schedule, as well as stockpile decisions. The company deployed an optimization AI that enabled operators to analyze and implement granular, actionable suggestions across the entire value chain and subsequently improve throughput.
End-to-end control towers help create organizational transparency through a weekly process involving three activities: cross-functional collaboration, inventory-performance tracking, and a locations review of specific stock-keeping units. Dashboards can be constantly refined based on user feedback to ensure they focus on the most important aspects of any given industry or sector. This end-to-end visibility can focus on any number of key functions—including inventory, demand, production, and customer service—and offers increasingly granular views within each function. Anticipated events with underlying AI technologies can also be displayed to flag risks to the operators.
For more on control towers and how they can improve supply chains, see the recent McKinsey article “Building a digital bridge across the supply chain with nerve centers.”
Most companies have a control tower serving as an operating nerve center. However, fully digital end-to-end control towers can increase resilience by expanding the scope of real-time monitoring to anticipate and respond to upcoming or potential supply-chain disruption. In this way, AI allows for enhanced end-to-end planning, giving historically isolated functions the benefit of full transparency. AI can also improve communication between partners across the value chain, enabling improved decision making and earlier detection and response to disruptions. Such transparency highlights the value of flexible demand: the more flexibility partners and internal stakeholders agree to, the more options the value chain has in reacting to challenges. Finally, the operating model can then be tailored to accommodate any new operational insights.
Enhancing end-to-end decision making with AI requires companies to think in terms of the concrete answers they want to obtain. For example, do you want a step-by-step action plan to help run your value chain? Is the goal to produce a go-no-go decision for investment based on normal conditions? Or are you primarily looking to ease communication and centralize decision making?
Determining the answers to these questions—and aligning them with stakeholders and operators—creates a shared strategy for the development phase. On this point, deploying value-chain AI requires a threefold approach encompassing value-driven solution design, enhanced business process and capability building, and seamless technological implementation (exhibit).
We strive to provide individuals with disabilities equal access to our website. If you would like information about this content we will be happy to work with you. Please email us at: [email protected]
- Value-driven solution design: Define which challenges each digital solution should address, who should be the primary user, and which process should benefit from the enabled technology.
- Enhanced business process and capability building: Redesign or enhance the business processes expected to benefit from new AI-enabled solutions. Improve data governance to facilitate high-quality data for enabling these AI solutions. Bring in expected end users to codesign AI solutions while upskilling them with the required technological capabilities.
- Seamless technological implementation: Begin by making the relevant data available. Ensure close collaboration among data scientists, operators, and stakeholders while building AI-enabled solutions. Develop user interfaces and user experiences (UI and UX) to support processes and integrate solutions into the organizational IT landscape.
Increasing supply-chain resilience is no longer a choice in many sectors—and AI has proven to be helpful with this goal. Yet shaping and successfully embarking on an AI-enabled supply-chain transformation journey requires a structured effort to prioritize the right set of use cases and gradually capture value. When implemented successfully, these solutions can enable a more accurate diagnosis of value-chain bottlenecks and risks with simulation techniques, better short- and long-term planning with optimization techniques, and a more proactive nerve center powered by AI.
Deploying the right AI capabilities to look deeply into an organization’s value chain can enable teams to quickly pivot while balancing efficiency and resilience. Armed with the right processes, organizations can create and adjust plans for the entire organization while keeping everyone aligned on risks and rewards. Operationally, AI capabilities can enable fact-based discussions across the entire value chain, which not only affects business processes but also results in better alignment across different business units.
Comments
0 comment